Reducción de la fricción en juntas dinámicas mediante tecnología láser
El desgaste por fricción en juntas dinámicas, ampliamente utilizadas en procesos industriales, provoca fugas y/o fallos prematuros y aumenta el consumo energético. El desafío de conseguir una reducción de fricción >20% en juntas dinámicas con un coste adicional <10% con respecto a procesos convencionales es posible mediante tecnología laser.
Una de las principales aplicaciones industriales dentro de la ingeniería son los sellos o juntas de caucho dinámicas, de amplio uso en la industria de automoción, aerogeneradores y aeronáutica, entre otros. Dichos componentes son una parte crítica en muchos dispositivos giratorios y deslizantes, dado que su principal función es la de evitar fugas mientras soportan millones de ciclos de carga en condiciones de altas oscilaciones. En consecuencia, el principal fenómeno que se produce es la fricción entre las superficies selladas.
La reducción de la fricción es un desafío constante ya que provoca la generación de calor, acelera el desgaste y causa daños y fugas prematuras, lo que aumenta el consumo de energía de los sistemas y afecta negativamente al rendimiento. Esta situación implica que los costes de mantenimiento se incrementan y que se producen situaciones de fallos catastróficos. Ante la necesidad de buscar soluciones industriales que consigan reducir la fricción en el comportamiento de juntas dinámicas, en el marco de una economía sostenible, surge el proyecto Mouldtex.
En ITAINNOVA desarrollamos nuevos materiales o mejoramos sus propiedades. ¿Quieres más información?
¿Cuál es el objetivo del proyecto?
El objetivo del proyecto es desarrollar y demostrar una metodología novedosa para el diseño y fabricación de grandes volúmenes de componentes poliméricos con superficies texturizadas, las cuales se diseñaran en función de las condiciones de operación de cada componente en particular. Con el diseño resultante se conseguirá una reducción de la fricción superior a un 20% por un coste extra de menos del 10%.
¿En qué consiste la metodología para la reducción de la fricción?
Se trata de grabar un micro-texturizado en ciertas superficies de la junta de sellado, técnica que provoca la reducción de la fricción entre un 20% y 50%, tal como se consolidó experimentalmente a nivel de laboratorio en investigaciones previas. Además, está comprobado que esta solución ingenieril no afecta a las propiedades funcionales del componente.
Al mismo tiempo que el micro-texturizado se postula como una técnica potencial para la reducción de la fricción, se identifican otras funciones básicas implícitas de la textura. Las micro-cavidades generadas mediante la aplicación del láser permiten atrapar restos de desgaste y actúan, al mismo tiempo, como depósito del lubricante habitualmente utilizado en los sistemas de sellado. Otra de las ventajas funcionales que aporta el texturizado es la mejora de la presión hidrodinámica entre las superficies en contacto. En último lugar, la micro-textura implica la reducción del área de contacto entre las superficies, de modo que se produce una reducción en la adhesión entre pares de contacto caucho y metal.
¿Cuáles son los desafíos iniciales?
Existen dos grandes fuentes de barreras tecnológicas relacionadas con el diseño de la textura y con el proceso de fabricación.
Respecto al diseño, se plantean desafíos en cuanto al cómo ha de ser la micro-textura. Ante el desconocimiento inicial, recurrir a un diseño basado en “prueba y error” se convertiría en un proceso extremadamente lento y costoso. La problemática es que no existe un enfoque uniforme para la optimización de un diseño de textura debido a la necesidad de adaptar el patrón seleccionado a cada tipo de sistema de contacto y condiciones de operación, lo cual es propio de cada aplicación. A su vez, la optimización habría de estar basada en aproximaciones matemáticas y herramientas numéricas capaces de modelar el fenómeno de la fricción y de optimizar el diseño, pero la complejidad matemática y física es elevada y no se dispone de modelos de simulación avanzados.
En cuanto al proceso de fabricación, es posible obtener juntas dinámicas micro-texturizadas mediante la aplicación directa de láser sobre la superficie del componente. Pero la producción en serie actual de juntas no incorpora esta tecnología y, por tanto, es necesario que estos micro-patrones se graben individualmente, junta a junta, en un proceso posterior independiente. Sin embargo, el post-proceso aplicado de forma individual en cada componente resulta inviable para procesos de producción en masa.
¿Cómo se superan las barreras tecnológicas?
Mouldtex plantea dos líneas de actuación:
- Desarrollar el potencial de la técnica del micro-texturizado para reducir la fricción y el desgaste de los componentes dinámicos de caucho. Se estima mejorar la fricción por encima de un 20% y disminuir el desgaste hasta alcanzar, como mínimo, duplicar la vida útil del componente.
- Implementar una técnica de fabricación novedosa y rentable en líneas de producción reales. En particular, la fabricación de las juntas micro-texturizadas se realiza mediante transferencia del micro-patrón desde la superficie del molde al componente. Es decir, la tecnología láser se aplica directamente en la superficie del molde una única vez, siendo en este caso necesario texturizar micro-protrusiones, en vez de micro-cavidades. Si bien la inversión en la fabricación del molde se incrementa, los costes no serán superiores al 10% con respecto a la fabricación convencional y los costes de inversión se deprecian en los miles de componentes fabricados con ese molde micro-texturizado.
¿Cuáles son las innovaciones clave?
Dentro de la extensa cadena de trabajo desde el cliente hasta el producto final, el proyecto desarrolla las siguientes innovaciones:
- Software de modelado avanzado para la identificación del patrón óptimo, para cada aplicación concreta, que produce una reducción de fricción significativa para las juntas de sellado.
- Software de diseño de moldes que aseguren un llenado adecuado y una correcta transferencia del patrón de la micro-textura del molde al componente.
- Sistema láser automatizado para la aplicación de patrones jerárquicos de micro-textura en el molde.
- Procedimiento de buenas prácticas para el moldeo y desmoldeo de los componentes basado en la aplicación de agentes desmoldeantes.
- Sistema de inspección óptica en línea para el control de calidad del patrón de la micro-textura superficial.
Se plantean varias líneas piloto para poner en valor los resultados del proyecto y comprobar que se produce una reducción de la fricción en componentes reales. Tras el diseño y fabricación de varios moldes, se fabricarán juntas rotativas y traslacionales.
¿Qué impacto tendrá en el mercado la metodología desarrollada y su consecuente reducción de fricción?
La tecnología desarrollada para la reducción de la fricción en juntas dinámicas se enfoca a multitud de sectores industriales donde los motores y equipamientos dinámicos son elementos clave, de modo que el impacto previsto en industrias como la automoción, transporte de gases y petróleo, aeronáutica o eólica, entre otros, es remarcable.
La metodología, por tanto, mejorará tanto el rendimiento como la eficiencia de los procesos ya que los tiempos de inactividad, provocados por paros destinados a mantenimiento o por la sustitución de componentes de sellado que han fallado, disminuirán al haberse producido una reducción de la fricción. Además, la fiabilidad en el sistema mejorará porque el mantenimiento necesario será menor.
En consecuencia, una vez amortizado el gasto que supone la inversión inicial, inferior a un 10% con respecto al coste de productos convencionales, la tecnología desarrollada en el proyecto Mouldtex se traduce en un ahorro en costes.
¿Tienes alguna idea o proyecto parecido? Ponte en contacto con nosotros o síguenos en nuestra newsletter.
Mouldtex es un proyecto enmarcado dentro del Programa H2020 de la Unión Europea, cuyo periodo de ejecución abarca desde noviembre de 2017 y abril de 2021. El proyecto está bajo la coordinación de ITAINNOVA y participan socios de ocho entidades adicionales: Gottfried Wilhelm Leibniz Universitaet Hannover (Alemania), Fundación para el Desarrollo de la Innovación y la Tecnología (España), Foundation For Research And Technology Hellas (Grecia), Orp Stampi Srl y Ml Engraving Srl (Italia), Optimal Optik Optikai Kft (Hungría), Skm Aeronautics (Israel) y Plastipolis (Francia).
Foto: www.mouldtex-project.eu
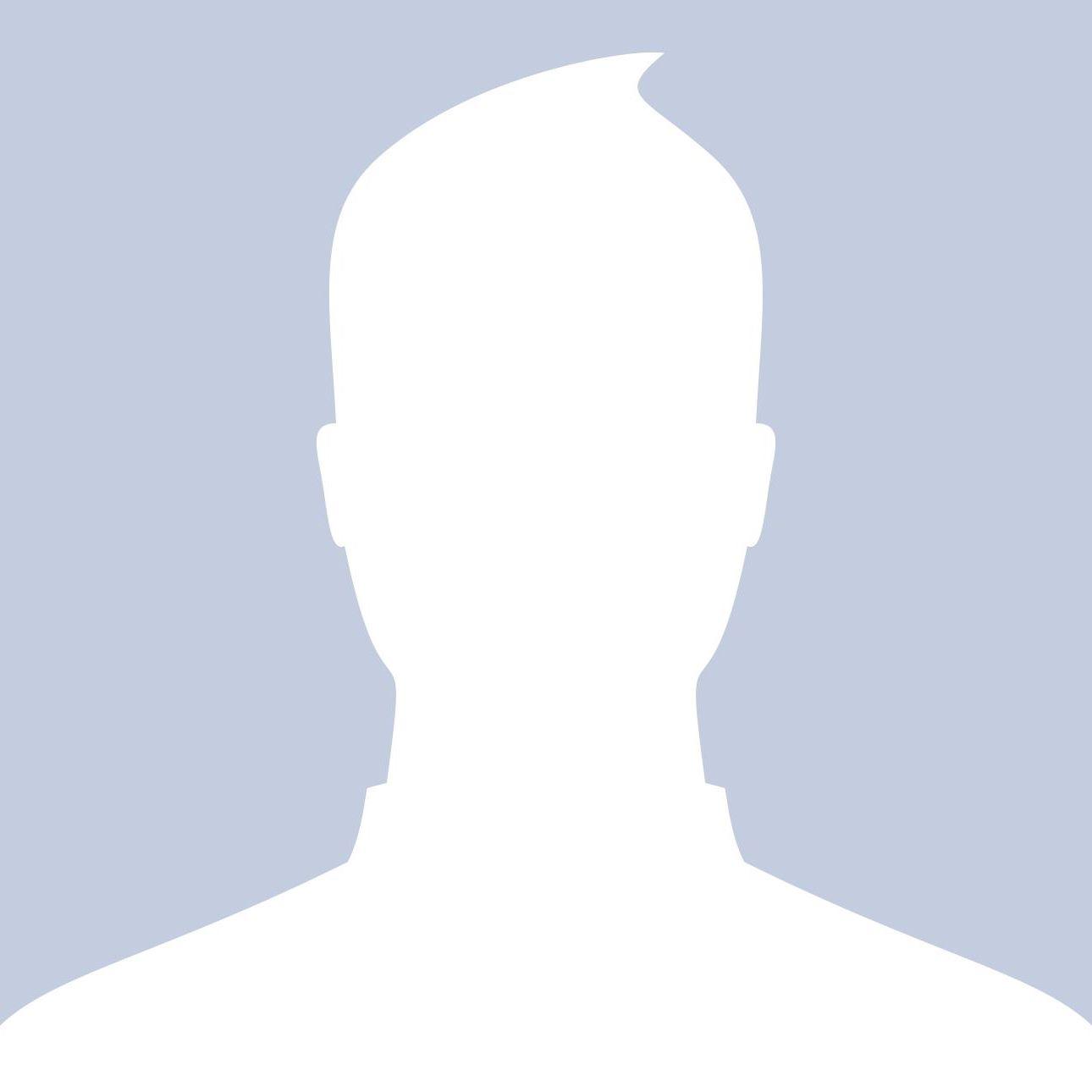
Belén Hernández
ARTÍCULOS DEL MÍSMO ÁMBITO
-
(II) Cómo implantar la IA en la fabricación de maquinaria para la construcción: Guía práctica
Viernes, 15 Noviembre 2024
- Industria 4.0
OTROS ARTÍCULOS
-
Componentes del coche eléctrico: Desarrollo e implicaciones técnicas
Viernes, 24 Enero 2025
- Diseño y desarrollo de vehículos eficientes