Monitorización de la salud estructural (SHM) en generadores de energía eólica
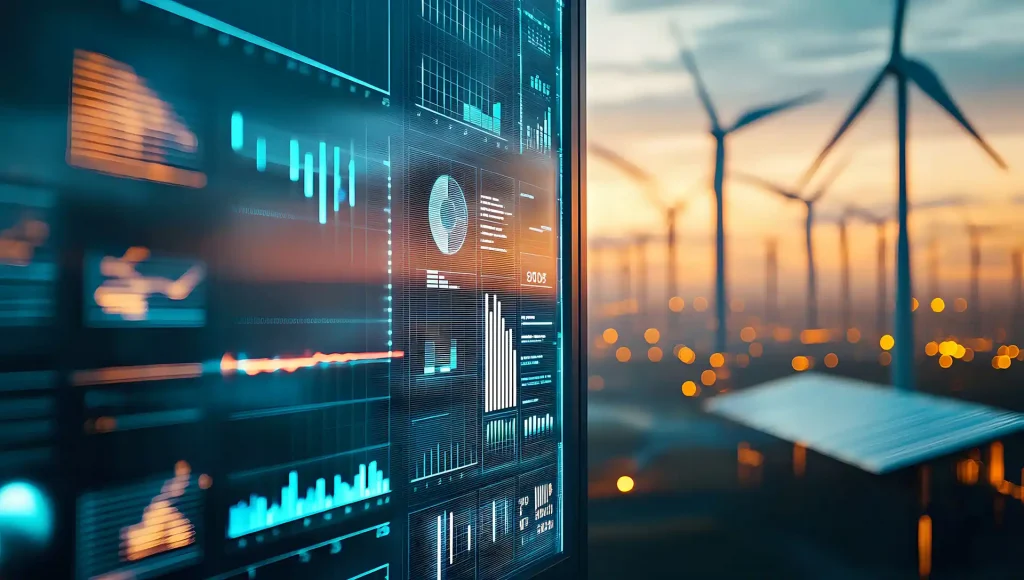
Introducción
Qué es la monitorización de la salud estructural (SHM)
La monitorización de la salud estructural (SHM) es una disciplina que combina sensores, tecnologías de datos y sistemas de análisis para evaluar de manera continua el estado de estructuras e infraestructuras críticas.
Al instalar sensores especializados en puntos estratégicos, el SHM permite captar información en tiempo real sobre el comportamiento y las condiciones de la estructura, proporcionando datos precisos sobre su integridad y ayudando a detectar daños o defectos antes de que se conviertan en un riesgo.
El SHM no se limita a una inspección puntual, sino que constituye un sistema de diagnóstico constante que detecta alteraciones en el estado de la estructura en sus diferentes fases de funcionamiento. Este enfoque permite una gestión mucho más proactiva, anticipando problemas y mejorando la gestión del mantenimiento al proporcionar información precisa sobre el estado de las estructuras.
En sectores como la aeronáutica, se empieza a hablar de ISHM (Integrated System Health Management), un concepto que va más allá del diagnóstico estructural, al prever cómo un daño estructural puede impactar en el rendimiento general de un sistema completo.
Además, el SHM favorece el aprovechamiento máximo de la vida útil de los componentes de forma segura, permitiendo una operación más eficiente y adaptada a las condiciones y necesidades específicas de cada sector.
Al aplicar el SHM, los operadores de parques eólicos pueden lograr un equilibrio entre seguridad y optimización de costes, reduciendo el número de intervenciones necesarias y limitando el impacto de las reparaciones sobre la actividad operativa. Es una tecnología que, más allá de la simple prevención, facilita una gestión sostenible de recursos y materiales a lo largo del ciclo de vida de una infraestructura.
Para obtener una explicación general sobre qué es el SHM, qué beneficios ofrece, en qué sectores industriales tiene aplicación y en qué etapas se divide el proceso, te invitamos a consultar este otro artículo de nuestro blog: ¿Qué es el SHM? Beneficios y aplicaciones del Structural Health Monitoring. En este caso, nos vamos a centrar en la aplicación del SHM específicamente a generadores de energía eólica.
Importancia del SHM en el sector de la energía eólica
En el ámbito de la energía eólica, la tecnología de SHM es fundamental para garantizar la seguridad, durabilidad y eficiencia de los aerogeneradores, estructuras que están sometidas a condiciones ambientales adversas y a cargas variables que generan un desgaste considerable.
Mediante el uso de SHM, es posible monitorizar en tiempo real componentes clave como las palas, la torre o el sistema de transmisión, detectando de manera preventiva cualquier signo de fatiga o daño.
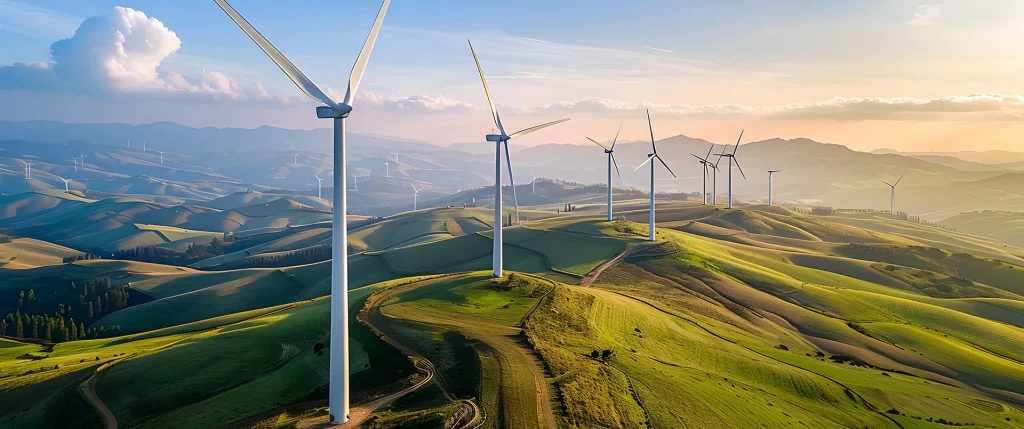
Si el SHM se fusiona, además, con un sistema de predicción de condiciones de operación (viento, temperatura, oleaje, etc.), éste puede servir como una fuente de información clave para el control de dichas operaciones, ya que podría establecer decisiones de compromiso entre la producción de energía y el desgaste de componentes en condiciones meteorológicas extremas.
Además, el uso de SHM contribuye a un modelo de gestión sostenible, ya que permite reducir el número de intervenciones, disminuyendo, tanto los costes operativos como el impacto ambiental. Esto es especialmente relevante en parques offshore, donde el coste de acceso a las instalaciones es muy alto.
Si bien este artículo se centra en los aerogeneradores, es importante señalar que la tecnología de SHM también es aplicable a otros sistemas de generación donde la durabilidad y resistencia de las estructuras también es esencial, como la energía mareomotriz.
Mantenimiento predictivo de aerogeneradores, un cambio de enfoque
El SHM transforma radicalmente el concepto de mantenimiento aplicado a los componentes y sistemas críticos de los generadores de energía eólica. Tradicionalmente, el mantenimiento se basaba en calendarios predefinidos o en la reparación de fallos tras su aparición. Sin embargo, con el uso del SHM, el mantenimiento predictivo emerge como un enfoque innovador que permite anticiparse a los fallos antes de que ocurran.
Esto se logra mediante la recopilación y análisis continuo de datos estructurales, que permiten detectar patrones de desgaste y predecir la evolución de daños en tiempo real. Gracias a tecnologías como los modelos de simulación basados en física y los gemelos digitales, los operadores pueden evaluar el impacto potencial de un daño en el rendimiento global del aerogenerador y planificar intervenciones precisas y eficientes. En definitiva, se trata de evolucionar el concepto de mantenimiento preventivo hacia uno de carácter predictivo.
Componentes, sistemas y procesos críticos de los aerogeneradores
Para comprender mejor cómo el SHM puede ayudar, tanto a los fabricantes de aerogeneradores, como a las empresas encargadas del mantenimiento de parques eólicos, es necesario primero identificar los componentes y sistemas clave de estos aparatos, así como los tipos de fallos, averías y desgastes a los que éstos suelen estar expuestos.
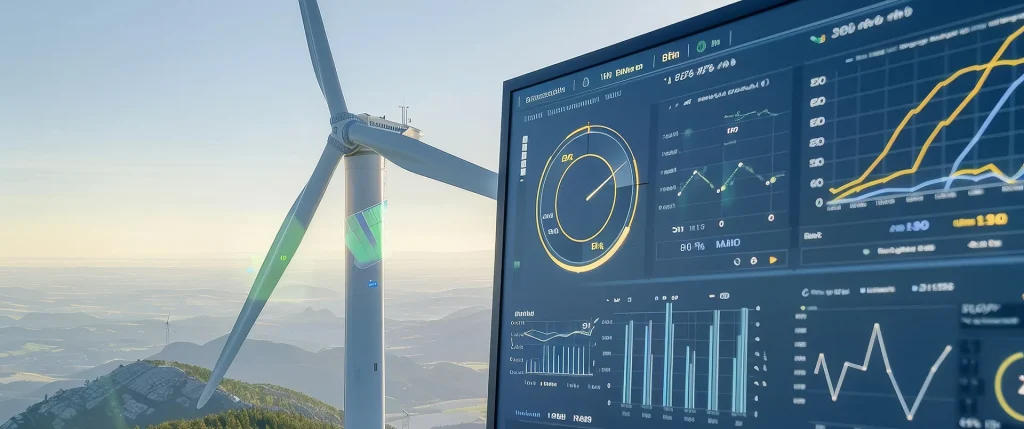
También exploraremos las fases o procesos que conforman el ciclo de vida de un aerogenerador, lo cual nos permitirá entender en qué etapas el SHM despliega su máximo potencial. Aunque el SHM se relaciona, principalmente, con el mantenimiento de los generadores en funcionamiento, desde las fases tempranas de diseño es posible seguir ciertas pautas y recomendaciones que facilitarán posteriormente una monitorización estructural efectiva y precisa.
Componentes y sistemas críticos de un generador eólico
- Rotor (palas y buje): El rotor es el conjunto que capta el viento y convierte su energía cinética en movimiento rotacional. Las palas, diseñadas para capturar la mayor cantidad posible de energía eólica, están sometidas a cargas variables y estrés constante, lo que puede provocar fatiga y desgaste. El SHM permite monitorizar en tiempo real las vibraciones y deformaciones en las palas, detectando signos tempranos de daño y asegurando que su estado no comprometa la eficiencia ni la seguridad del sistema.
- Góndola (generador y caja de engranajes): La góndola alberga los principales componentes mecánicos y eléctricos del aerogenerador. Dentro de ella, el generador convierte la energía mecánica en electricidad, mientras que la caja de engranajes (o multiplicadora) ajusta la velocidad de rotación del rotor a la velocidad adecuada para el generador. Estos elementos están expuestos a vibraciones constantes y fricción, lo que puede ocasionar desgaste y fallos mecánicos. La SHM en la góndola se centra en monitorizar las vibraciones y el estado de la caja de engranajes y el generador, anticipando desgastes que puedan afectar el rendimiento y permitiendo planificar el mantenimiento preventivo.
- Sistema de control (orientación y frenado): Este sistema monitoriza y ajusta el funcionamiento del aerogenerador, asegurando que siempre opere en condiciones óptimas y seguras. El sistema de orientación ajusta la posición de la góndola para optimizar la captación de energía, mientras que el sistema de frenado desacelera o detiene el rotor en condiciones de viento extremo, protegiendo los componentes de posibles daños. La SHM en el sistema de control permite asegurar que la orientación y el frenado funcionen correctamente, monitorizando su efectividad y detectando posibles fallos antes de que representen un riesgo para el sistema.
- Torre: La torre es la estructura que sostiene el rotor y la góndola a una altura adecuada para captar el viento de manera efectiva. Su resistencia y estabilidad son críticas, ya que soporta tanto el peso de los componentes como las cargas de viento. El SHM en la torre permite monitorizar las tensiones y las vibraciones que afectan a su estructura, en particular en instalaciones offshore, donde también enfrenta la corrosión y el movimiento del oleaje. Esto ayuda a prevenir fallos estructurales y a planificar el mantenimiento de manera precisa.
- Base o cimentación: En aerogeneradores offshore, la base es fundamental para garantizar la estabilidad de toda la estructura frente a condiciones marinas extremas, como la salinidad y el constante movimiento del agua. La SHM monitoriza la integridad de la cimentación, detectando signos de desgaste o corrosión en sus materiales y asegurando que la estructura pueda soportar las cargas sin riesgo de fallo.
Tecnologías clave del SHM aplicado a sistemas y componentes de aerogeneradores
La monitorización de la salud estructural (SHM) en aerogeneradores emplea un conjunto de tecnologías avanzadas que permiten captar datos en tiempo real y realizar un análisis profundo de las condiciones estructurales.
Estas tecnologías permiten anticipar fallos y optimizar el mantenimiento, mejorando la eficiencia y vida útil de cada componente. A continuación, se presentan las principales tecnologías empleadas en SHM y su aplicación directa en los sistemas y componentes críticos de los aerogeneradores.
Técnicas de inspección basadas en ultrasonidos
Aplicación: Inspección de materiales y componentes críticos, como las palas y los elementos del sistema de transmisión.
Función: Estas técnicas permiten detectar defectos internos no visibles, como grietas o inclusiones, mediante la transmisión y análisis de ondas ultrasónicas. En el contexto del SHM, los ultrasonidos se utilizan para identificar daños en las estructuras antes de que sean detectables por otros métodos, complementando la información obtenida de los sensores instalados en el aerogenerador.
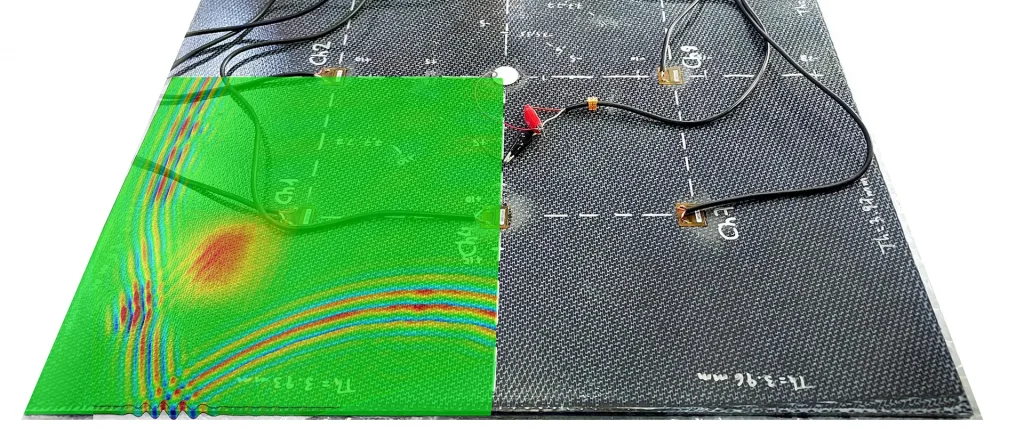
Beneficio específico: Aportan un nivel adicional de precisión en la identificación temprana de fallos, especialmente en materiales compuestos y componentes de alta complejidad. Esto permite a los técnicos evaluar la gravedad del daño y tomar decisiones informadas sobre el mantenimiento necesario, evitando costosos reemplazos prematuros.
Modelos de simulación basados en la física
- Aplicación: Todos los componentes estructurales del aerogenerador (palas, torre, cimentación y sistema de transmisión).
- Función: Estos modelos permiten evaluar el estado estructural de los componentes y predecir su vida útil restante. Integran los datos recogidos por los sensores de SHM y los combinan con principios físicos para simular cómo evolucionará un daño específico (como grietas, corrosión o delaminación). Esto genera un gemelo digital que permite analizar el comportamiento futuro de los fallos detectados y evaluar posibles soluciones de forma virtual.
- Beneficio específico: Proporcionan a los operadores de parques eólicos una herramienta avanzada para planificar intervenciones de mantenimiento de forma precisa y segura, maximizando el rendimiento del aerogenerador. Además, permiten optimizar los recursos, evitando intervenciones innecesarias y extendiendo el tiempo de operación de los componentes afectados.
Sensores de vibración y deformación
Aplicación: Palas, torre y sistema de transmisión.
Función: Los sensores de vibración y deformación son esenciales para capturar datos sobre el comportamiento dinámico de las palas, la torre y los elementos de transmisión. Estos sensores miden con precisión las frecuencias de vibración y las deformaciones sufridas en cada componente debido a las cargas cíclicas y variables que se presentan en condiciones de viento cambiantes.
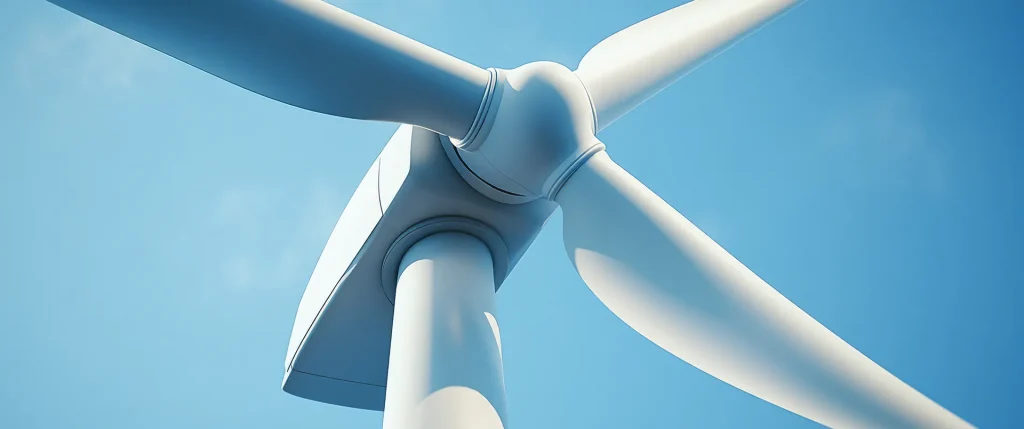
Beneficio específico: Al captar pequeñas variaciones en los patrones de vibración y deformación, los sensores permiten identificar problemas como la aparición de grietas o áreas con fatiga estructural antes de que sean visibles. Por ejemplo, en las palas, las fluctuaciones anómalas en los datos de vibración pueden indicar zonas de acumulación de estrés, lo que permite a los técnicos ajustar los planes de mantenimiento y reforzar las áreas críticas. En el sistema de transmisión, donde el desgaste por fricción es constante, estos sensores ayudan a detectar la aparición de holguras y desajustes, optimizando el rendimiento y reduciendo el riesgo de fallos imprevistos.
Sensores ambientales y de corrosión
Aplicación: Torre y base, especialmente en entornos offshore.
Función: En instalaciones offshore, las condiciones ambientales adversas, como la humedad y la salinidad, aceleran el desgaste de los componentes. Los sensores de corrosión y ambientales están diseñados para medir variables críticas como la concentración de sal en el aire, la humedad relativa y los niveles de corrosión superficial en puntos sensibles de la torre y la cimentación. Estos datos permiten evaluar el impacto del entorno en tiempo real, ajustando las rutinas de mantenimiento y tomando medidas preventivas específicas en zonas de alto riesgo.
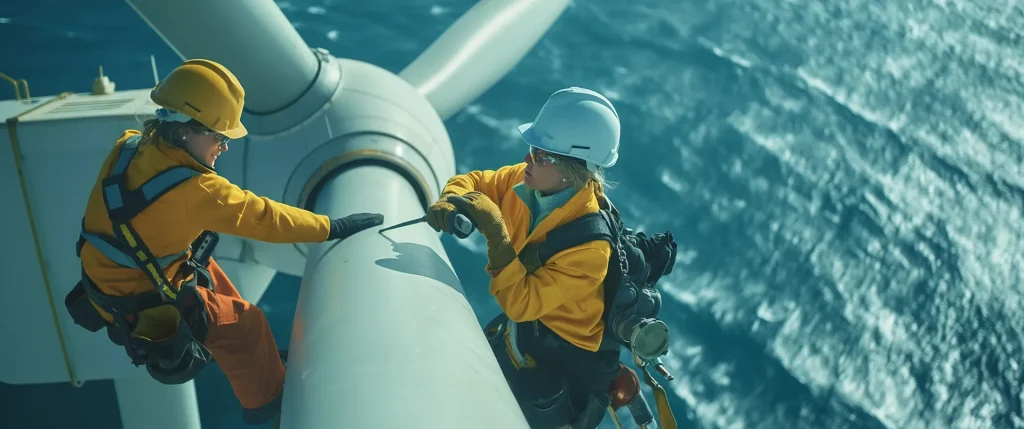
Beneficio específico: Estos sensores ayudan a establecer patrones de corrosión a lo largo del tiempo y a realizar un seguimiento preciso de la degradación de materiales, en especial en la torre y en los sistemas de anclaje de la base. Esto permite a las empresas implementar recubrimientos anticorrosivos o tratamientos específicos en momentos clave, optimizando tanto el coste como la efectividad de la protección. En las cimentaciones offshore, donde los niveles de corrosión y desgaste son difíciles de inspeccionar, los datos obtenidos permiten planificar las intervenciones sin necesidad de revisiones físicas frecuentes.
Análisis de datos y Machine Learning
Aplicación: Generador, sistema de transmisión y palas.
Función: El análisis de datos de SHM en aerogeneradores se basa en algoritmos de Machine Learning (ML) que identifican patrones de desgaste en los componentes clave. Estos algoritmos, a partir de datos históricos y de condiciones de funcionamiento en tiempo real, logran prever la evolución de posibles defectos en el generador, en las palas y en el sistema de transmisión. Por ejemplo, los modelos predictivos analizan las variaciones en el comportamiento de la máquina, señalando cuándo es probable que se produzcan fallos debido a la fatiga o al desgaste excesivo.
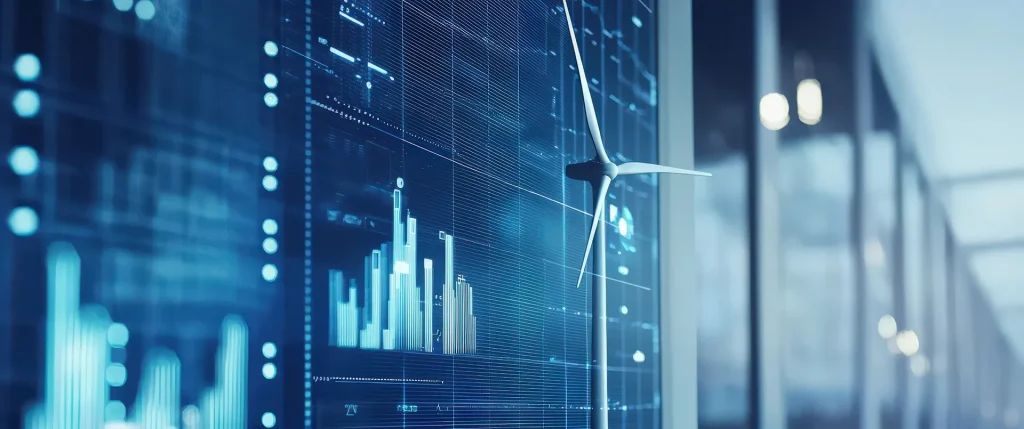
Beneficio específico: La capacidad de predecir fallos antes de que ocurran es un valor crítico, ya que permite coordinar intervenciones de mantenimiento y prevenir paradas no planificadas. En el generador, el machine learning ayuda a identificar variaciones en el consumo de energía o en el nivel de fricción, detectando problemas de eficiencia o desgaste mecánico. Para las palas, estos modelos también permiten hacer un seguimiento continuo de su exposición a condiciones de viento extremas, anticipando los puntos en los que podría producirse delaminación o fractura. Esto aumenta la seguridad y la disponibilidad de la turbina, a la vez que optimiza la gestión de recursos.
Redes IoT para monitorización remota
Aplicación: Todos los componentes del aerogenerador.
Función: La integración de los sensores de SHM en redes IoT permite acceder de forma remota a los datos recopilados en cada componente del aerogenerador. Este acceso en tiempo real es fundamental en entornos offshore, donde el mantenimiento y las inspecciones físicas son complejas y costosas. Las redes IoT no solo recogen datos de cada sensor, sino que los transmiten en tiempo real a una plataforma central, donde se analizan y visualizan para la toma de decisiones.
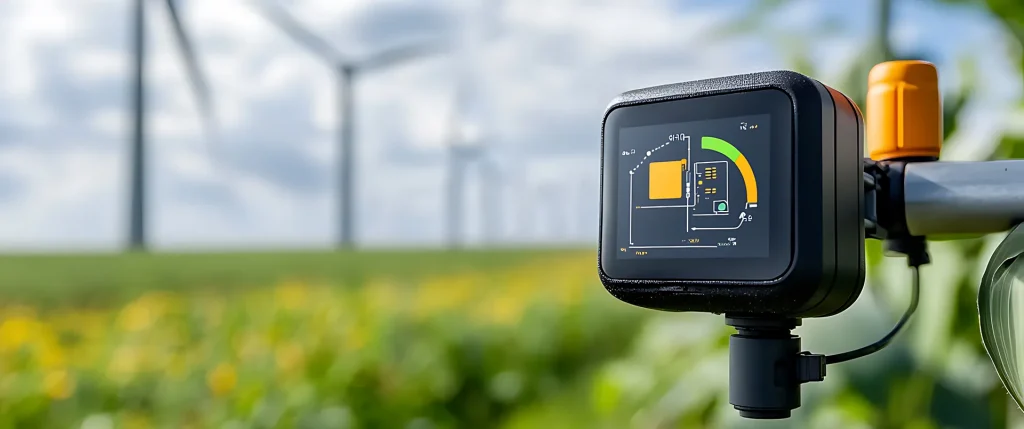
Beneficio específico: Las redes IoT permiten un monitoreo centralizado de múltiples aerogeneradores en diferentes ubicaciones, optimizando el control y facilitando una respuesta inmediata ante cualquier cambio inesperado en el estado de los componentes. En las instalaciones offshore, la monitorización remota reduce la necesidad de desplazamiento de personal técnico y permite una gestión proactiva basada en datos concretos, minimizando los tiempos de inactividad y optimizando los recursos de mantenimiento.
Aportaciones del SHM a la circularidad y la sostenibilidad
La monitorización de la salud estructural (SHM), no sólo optimiza la operación y el mantenimiento de los aerogeneradores, sino que también contribuye significativamente a los objetivos de sostenibilidad, circularidad y medioambientales. A continuación, se destacan las principales formas en que el SHM apoya estos principios eco-friendly:
Uso de materiales funcionales y biobasados
La elección de materiales sostenibles en los componentes de aerogeneradores es fundamental para reducir el impacto ambiental del ciclo de vida. Los materiales biobasados, como los polímeros reforzados con fibras naturales, pueden sustituir componentes de origen fósil en elementos como las palas.
El SHM permite monitorizar el rendimiento de estos materiales, asegurando que cumplan con los estándares de durabilidad y seguridad, y detectando posibles signos de desgaste prematuro o fatiga. Esto facilita la validación y optimización de materiales sostenibles en condiciones operativas reales, permitiendo su adopción generalizada en la fabricación de aerogeneradores.
Optimización de la circularidad y reciclabilidad
En el contexto de la economía circular, el SHM juega un papel importante al proporcionar datos precisos sobre el estado de cada componente a lo largo de su vida útil. Esto permite evaluar la condición estructural al final del ciclo de vida, determinando qué piezas pueden ser reutilizadas o recicladas.
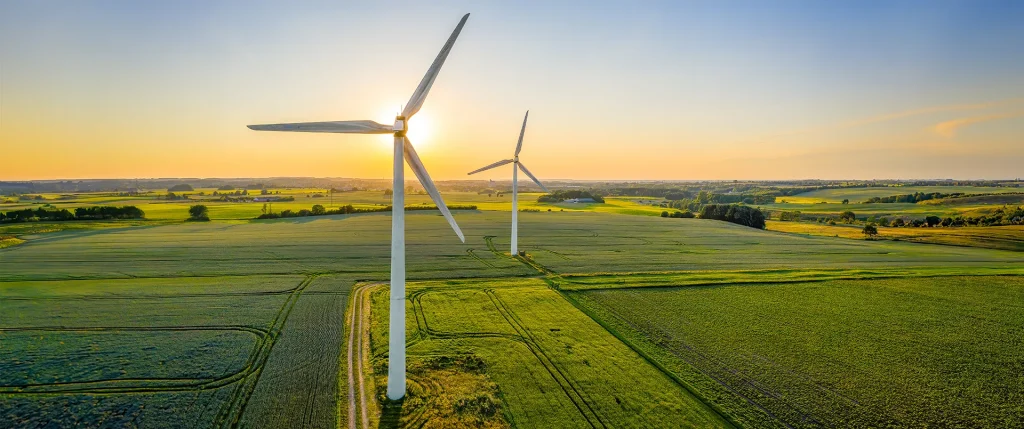
En concreto, el SHM facilita la identificación de palas, cojinetes o partes de la torre que, tras su evaluación estructural, pueden ser reacondicionados y reinsertados en el ciclo de producción, evitando la necesidad de fabricar nuevas piezas y reduciendo el consumo de materias primas.
Optimización de recursos y prolongación de la vida útil
Uno de los aspectos más sostenibles del SHM es su capacidad para anticipar problemas y reducir las intervenciones de mantenimiento innecesarias. Al predecir el momento exacto en que un componente requiere atención, el SHM ayuda a evitar desplazamientos y el uso excesivo de recursos, especialmente en instalaciones offshore donde el mantenimiento implica un coste elevado y un impacto ambiental considerable.
Esto, no sólo optimiza los costes operativos, sino que también contribuye a la neutralidad climática al minimizar el impacto logístico y las emisiones asociadas al transporte de personal y materiales.
Además, al extender la vida operativa del aerogenerador, se maximiza la generación de energía limpia sin necesidad de aumentar la capacidad de producción, contribuyendo a los objetivos de sostenibilidad.
En resumen, a través de todas estas aportaciones, el SHM se consolida como una herramienta clave para promover la sostenibilidad en el sector de la energía eólica, mejorando tanto la eficiencia operativa como el impacto ambiental de cada aerogenerador.
Soluciones tecnológicas y casos de éxito del ITA
En el ITA ofrecemos diversas soluciones tecnológicas que apoyan el desarrollo de aerogeneradores más eficientes, sostenibles y duraderos. Veamos algunas de ellas.
Simulación computacional
El equipo de Materiales y Componentes del ITA tiene una sólida experiencia en la aplicación de modelos de simulación computacional basados en principios físicos para la evaluación estructural y la predicción de la vida útil de los componentes.
Estas simulaciones permiten integrar los datos recogidos por los sensores de SHM y analizar en detalle la progresión de daños como grietas, corrosión o delaminación. A través de esta tecnología, se generan gemelos digitales que replican virtualmente el comportamiento de las estructuras en condiciones reales, permitiendo evaluar el impacto de los daños detectados y predecir su evolución en el tiempo.
Todo ello es clave a la hora de optimizar los recursos y tomar decisiones basadas en datos sobre la reparación o reemplazo de componentes, asegurando la máxima seguridad y eficiencia operativa de los aerogeneradores.
Sensores integrados y redes de monitorización personalizadas
Diseñamos sistemas de sensores inteligentes para multitud de sectores y ámbitos. En el caso de los aerogeneradores, éstos se integran en puntos estratégicos, como las palas, la torre y el sistema de transmisión, permitiendo capturar datos de vibración, deformación y otros factores clave en tiempo real. Esto facilita una monitorización continua y permite detectar posibles fallos antes de que se conviertan en problemas graves.
Modelos predictivos de mantenimiento basados en machine learning
El ITA emplea algoritmos de machine learning para analizar los datos recogidos por los sensores de SHM. Esto permite identificar patrones de desgaste en los componentes y prever fallos antes de que ocurran, facilitando una planificación de mantenimiento optimizada y reduciendo los tiempos de inactividad.
Soluciones IoT para monitorización remota en entornos extremos
Las soluciones de IoT del ITA permiten la monitorización remota de los aerogeneradores, especialmente útil en instalaciones offshore de difícil acceso. Estas soluciones aseguran una supervisión continua y en tiempo real, facilitando el mantenimiento a distancia y reduciendo la necesidad de visitas físicas a las instalaciones.
Generación eléctrica y sistemas sostenibles
Aunque no está directamente relacionada con el SHM, es interesante nombrar nuestra solución tecnológica para la generación eléctrica y sistemas sostenibles, ya que se centra en el diseño de sistemas eléctricos y de almacenamiento eficientes y sostenibles para aplicaciones de generación de energía.
La implementación de sistemas de generación eléctrica bien diseñados complementa el SHM al asegurar que los componentes eléctricos del aerogenerador, como el generador y los sistemas de control, funcionen de manera estable y eficiente. Esto reduce la carga de trabajo en los sistemas mecánicos y estructurales, optimizando el rendimiento general del aerogenerador y extendiendo su vida útil.
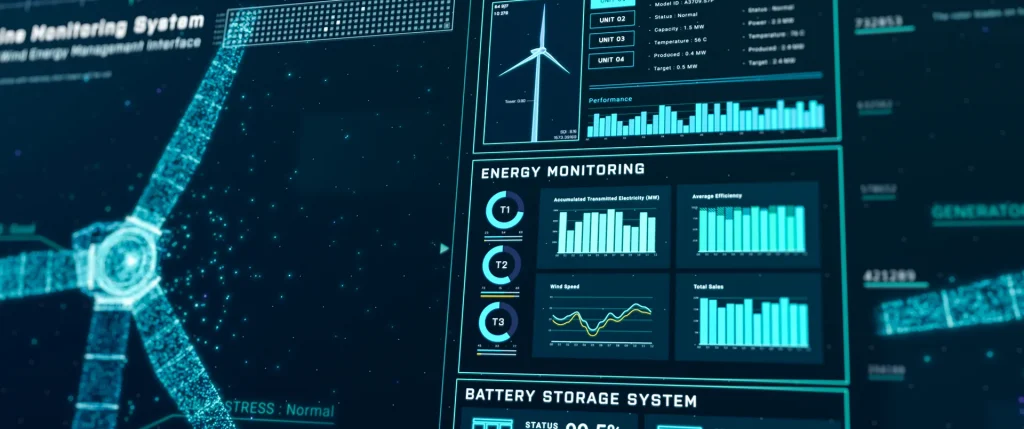
Veamos ahora algunos casos de éxito basados en las soluciones anteriormente mencionadas:
CARBO4POWER
El ITA participa en el proyecto europeo Carbo4Power, cuyo objetivo principal es desarrollar una nueva generación de palas para aerogeneradores offshore más ligeras y resistentes, combinando múltiples materiales y buscando multifuncionalidad, modularidad, ligereza, la integración de técnicas de monitorización estructural (SHM) y una mayor durabilidad,
WINDTURBARS
Este proyecto se centra en el desarrollo de soluciones de mantenimiento predictivo específicamente para aerogeneradores. WINDTURBARS utiliza herramientas de SHM e inteligencia artificial para predecir y prevenir fallos, optimizando el tiempo de funcionamiento y reduciendo costes de operación.
WINDTURBARS
Otros sectores
Además del sector energético, el ITA ha desarrollado proyectos de SHM con gran éxito en otros sectores como el aeronáutico (Proyecto LEVIS) o la automoción (Proyecto GENEX). En el caso de GENEX, el ITA es además el coordinador del proyecto, cuyo objetivo es desarrollar una metodología novedosa impulsada por gemelos digitales y basada en modelos mejorados que integran el conocimiento interdisciplinario del ciclo de vida de la aeronave, desde la fabricación hasta la operación en servicio, incluidos los procesos de reparación, para respaldar la optimización y la ecoeficiencia.
Conclusión
La monitorización de la salud estructural (SHM) se ha convertido en una herramienta fundamental para maximizar la eficiencia, la durabilidad y la sostenibilidad de los aerogeneradores en el sector de la energía eólica. Gracias al SHM, es posible anticiparse a los problemas estructurales de los componentes críticos, optimizar el mantenimiento predictivo y reducir los costes operativos a lo largo del ciclo de vida de estas instalaciones.
Además, la implementación de tecnologías avanzadas de SHM permite contribuir a la circularidad y al uso eficiente de los recursos, alineándose con los objetivos de sostenibilidad del sector.
En el ITA estamos comprometidos con el desarrollo de soluciones tecnológicas adaptadas a las necesidades de los fabricantes y operadores de aerogeneradores, tanto en instalaciones onshore como offshore: sensores de última generación, modelos predictivos basados en machine learning, redes IoT para monitorización remota, desarrollo de nuevos materiales, etc.
Si eres responsable de I+D en una empresa del sector eólico y deseas mejorar la fiabilidad y sostenibilidad de tus aerogeneradores, te invitamos a conocer más sobre nuestras soluciones tecnológicas y casos de éxito:
Contacta con nosotros
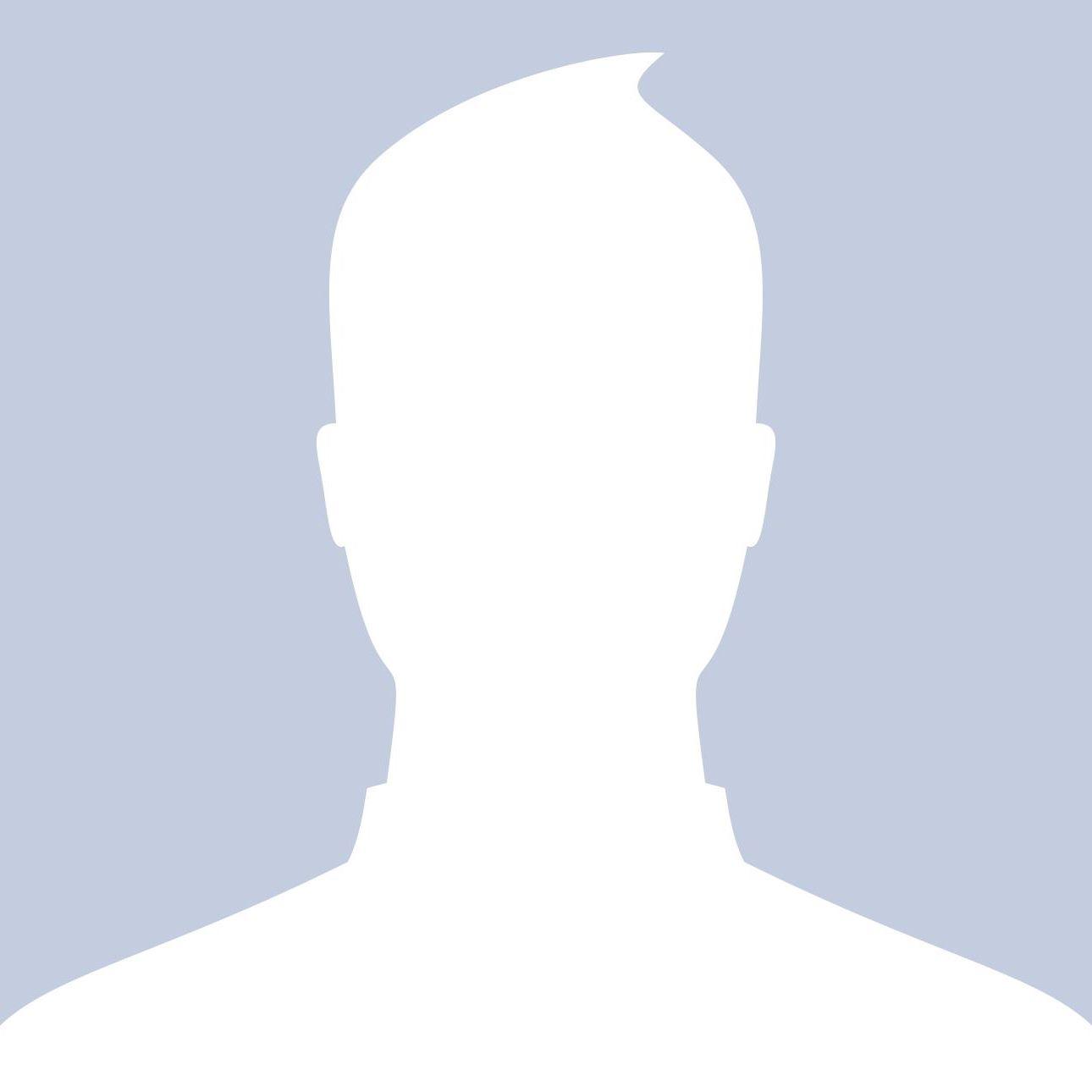
Artículo validado por Ana Martínez (Desarrollo de Negocio) y Andrea Calvo (Materiales y Componentes)
ARTÍCULOS DEL MÍSMO ÁMBITO
-
Comunidades energéticas: beneficios de la IA para la producción y gestión de la energía
Martes, 25 Junio 2024
- Sistemas de generación eficientes
OTROS ARTÍCULOS
-
Componentes del coche eléctrico: Desarrollo e implicaciones técnicas
Viernes, 24 Enero 2025
- Diseño y desarrollo de vehículos eficientes