Prim-Rock busca reducir la huella de carbono y aumentar la eficiencia energética de la industria metalúrgica y cementera
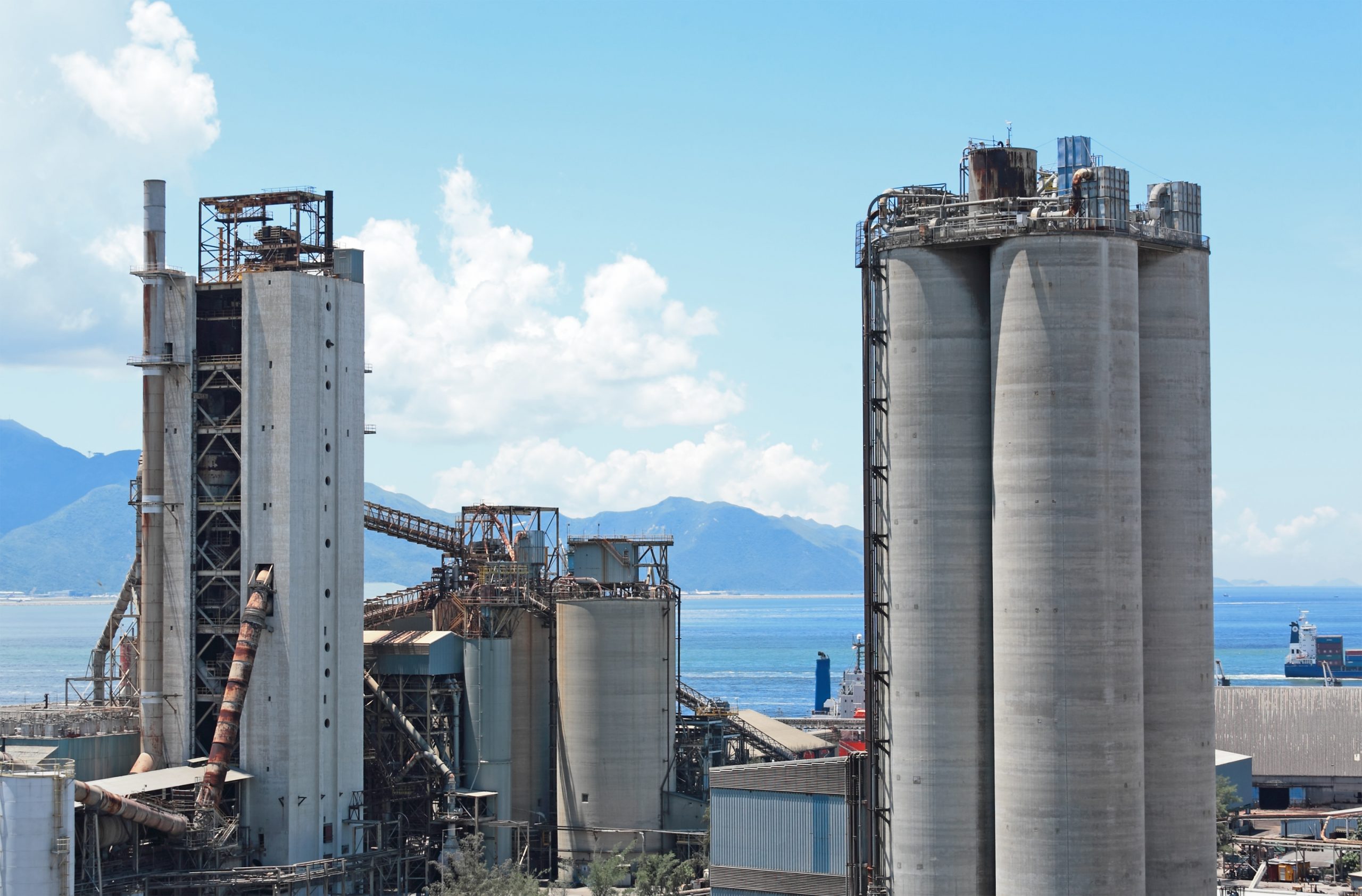
Esta semana se celebra en Atenas (Grecia) la primera reunión de socios del proyecto Prim-Rock, financiado por la Unión Europea, dentro del programa: HORIZON-CL4-2024-TWIN-TRANSITION-01, en el que participa el Instituto Tecnológico de Aragón ITA.
Liderado por ETHNICON METSOVION POLYTECHNION, la Universidad Politécnica Nacional de Atenas; participan en Prim-Rock 22 socios de 8 países diferentes (Grecia, Reino Unido, España, Bélgica, Italia, Polonia, Austria, Lituania). Son 8 pymes, 6 centros tecnológicos, 3 universidades y 5 grandes empresas.
Este proyecto, que celebra su reunión de lanzamiento, finalizará en septiembre de 2028 y busca reducir la huella de carbono y aumentar la eficiencia energética de la industria metalúrgica y cementera.
Las industrias metalúrgicas y cementeras son actualmente unas de las más contaminantes por su nivel de emisiones de CO2, además de generar un elevado volumen de residuos. El proyecto Prim-Rock va a desarrollar y demostrar tecnologías que sienten las bases de un procesado de minerales más sostenible, eficiente y con menos huella de carbono.
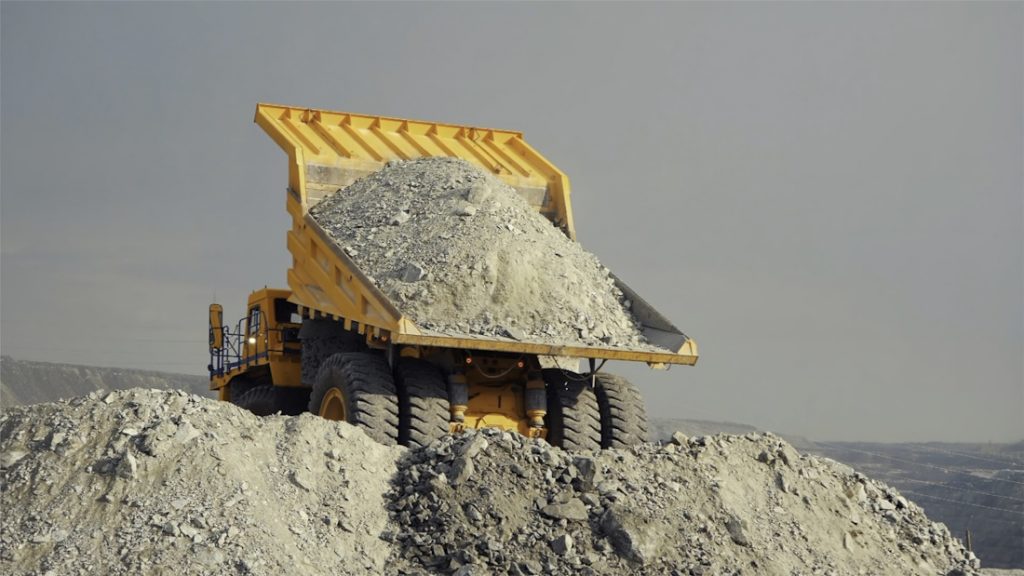
Se van a montar dos unidades piloto, una en Grecia para el proceso de calcinación para el tratamiento de caliza y magnesita con el sistema MRI y el IFRK, y otra en España para el proceso de tostado para el tratamiento de laterita, blenda y calcopirita, con el sistema MRI, el lFRK y el MRK. Hay cinco casos de uso con cinco minerales, pertenecientes a tres sectores SPIRE: caliza (sector cementero), magnesita, laterita (ambos del sector minerales), calcopirita y blenda (sector de metales no férricos).
Carmen Alfaro, del equipo de Integridad estructural y fatiga, del Departamento de Materiales y Componentes, es la responsable del proyecto en el ITA. Explica que "en Prim-Rock se desarrollará una tecnología para hornos rotativos de combustión indirecta electrificados (IFRK), en los que el horno se calienta desde el exterior, mediante una cubierta térmica, y el material se calienta a través del contacto con la carcasa caliente del horno. Por lo tanto, los IFRK pueden tratar todos los rangos de granulometría, incluidos los sólidos finamente divididos, ya que no están en contacto íntimo con los gases de combustión calientes. Como resultado, se minimizan las pérdidas de materia prima. Además, los IFRK pueden proporcionar el entorno controlado necesario para un procesamiento eficaz del material, como la ausencia de oxígeno a altas temperaturas y la utilización de un entorno reductor libre de oxígeno. Como la fuente de calor es externa, el método de calentamiento indirecto permite un control preciso de la temperatura y proporciona una distribución de calor más uniforme, minimizando el riesgo de sobrecalentamiento localizado o gradientes térmicos dentro del material".
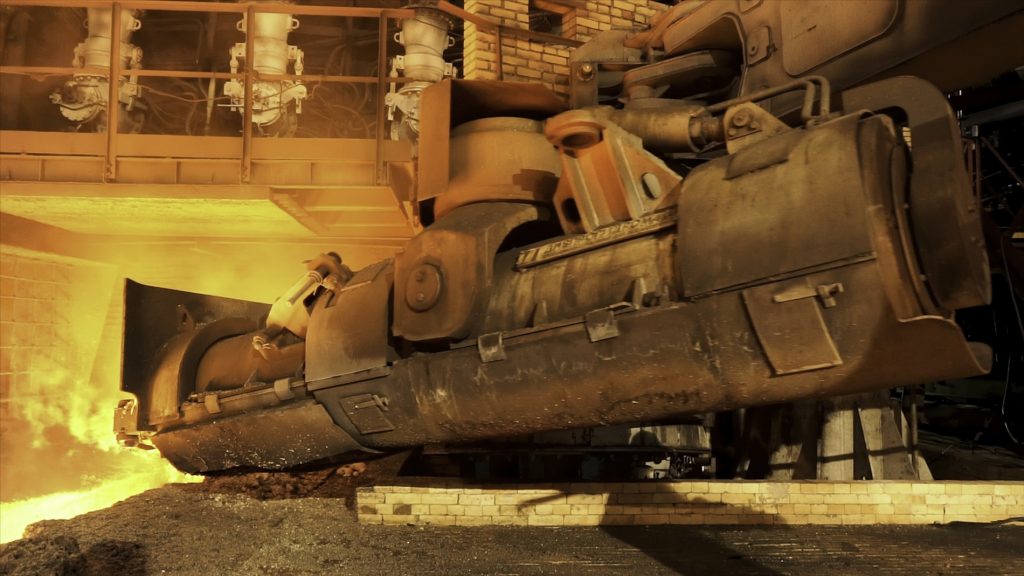
Además, el desarrollo del proyecto Prim-Rock incluye la construcción de un horno microondas para el proceso de reducción de sulfuros metálicos, diseñado con campos electromagnéticos ajustables dentro del tubo y con un novedoso sistema capaz de modular la señal para adaptarse a los cambios dinámicos que ocurren durante la reacción de tostado. Esta innovación es crucial para gestionar la transición de materiales de propiedades dieléctricas moderadamente bajas a estados conductores, lo que requiere un control preciso del campo eléctrico en un reactor diseñado para materiales metálicos. Un sistema de control avanzado recopilará datos de propiedades térmicas y de microondas, que serán fundamentales para desarrollar el software necesarios para el ajuste en tiempo real del proceso. Este nivel de control es esencial para optimizar la reacción de tostado y asegurar un tratamiento eficiente de los materiales.
Papel del ITA
El ITA se va a encargar de la simulación numérica del proceso de tostado. Se va a estudiar la reacción química utilización técnicas de simulación de dinámica molecular. El modelo de reacción química se va a integrar en un modelo de fluidodinámica computacional con partículas discretas (CFD-DEM) a pequeña escala, que estudiará la influencia de las variables físicas y propiedades de los minerales en el rendimiento de la reacción. Este modelo a escala de partículas se implementará en modelo termofísico del reactor completo (llevada a cabo por la Universidad Brunel de Londres), por lo que es una herramienta fundamental para el escalado.
En una segunda etapa, se utilizará el modelo termofísico del tostado en el IFRK para realizar un diseño de experimentos que estudiará el proceso bajo diferentes condiciones y a partir de los resultados, ITA construirá un modelo de orden reducido del proceso, que servirá posteriormente para la optimización de los parámetros del proceso.
Uso de Hidrógeno
El hidrógeno proporciona una atmósfera reductora necesaria para la extracción de los metales de sus correspondientes óxidos, sustituyendo el carbón, que ha sido el agente reductor más utilizado históricamente por su abundancia y bajo coste. En el camino de la industria hacia la descarbonización, el hidrógeno es una fuente sostenible tanto para la producción de energía como para su utilización como agente reductor en la producción de metal. Además, tiene otras ventajas, como la falta de contaminantes asociados al uso de carbón y coque, la temperatura de reducción es más baja y permite la utilización de reactores continuos, explica Carmen Alfaro.
Aunque la reducción de óxidos de metal con hidrógeno se ha estudiado ampliamente a escala de laboratorio, hay retos por resolver. La reducción de sulfuros, que son una fuente significativa de minerales críticos, produce ácido sulfhídrico, un gas muy tóxico (la reducción de óxidos produce agua). Además, los modelos termodinámicos que estudian las reacciones involucradas no están todavía lo suficientemente desarrollados, no hay suficientes datos experimentales para el escalado del proceso a escala piloto (y posteriormente industrial), no se conoce el impacto de los pretratamientos de los minerales en la eficiencia de la reducción con hidrógeno y no se ha analizado la viabilidad económica del proceso consideran los costes del hidrógeno. En general, el proceso se encuentra todavía en fase de prueba de concepto.
Respecto a la seguridad, en este proyecto se trabaja con IFRK y MRK, que, a diferencia de los DRK, proporcionan un entorno controlado reductor libre de oxígeno en el interior del reactor. En ausencia de oxígeno, el hidrógeno, aunque sea a alta temperatura, no entraña riesgos. Ya hay otros casos industriales donde ya se está utilizando el hidrógeno como reductor. Es decir, la tecnología propuesta se centra en un nuevo tipo de reactor, pero no involucra nuevos riesgos añadidos.
En general, el mayor reto de descarbonizar la industria del acero es la adaptación de las estructuras de hornos ya existentes al uso del hidrógeno.
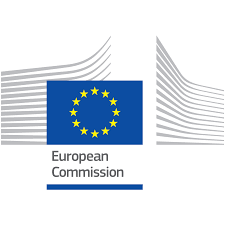
En prensa: heraldo.es
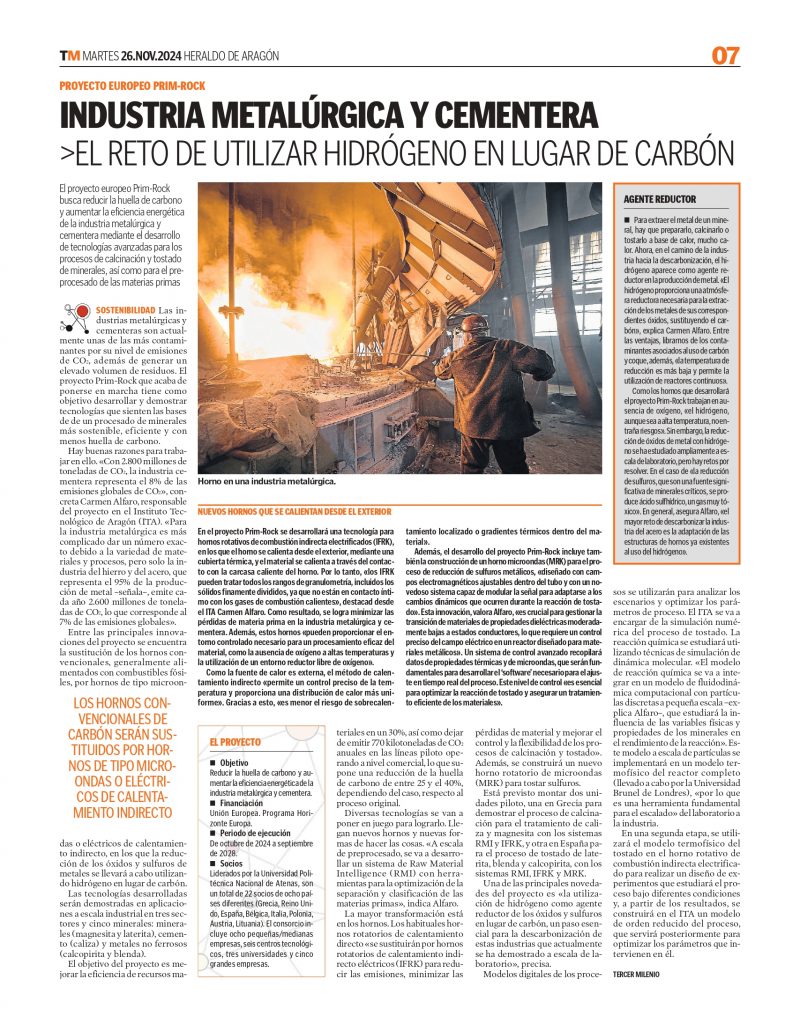
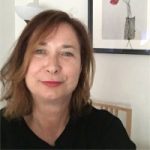
Lourdes Buisán Gabás
ARTÍCULOS DEL MÍSMO ÁMBITO
-
ITA | Viernes, 07 Marzo 2025
OTROS ARTÍCULOS
-
El ITA asiste al Foro Europeo para la Ciencia, Tecnología e Innovación
ITA | Jueves, 13 Marzo 2025